Cargo news
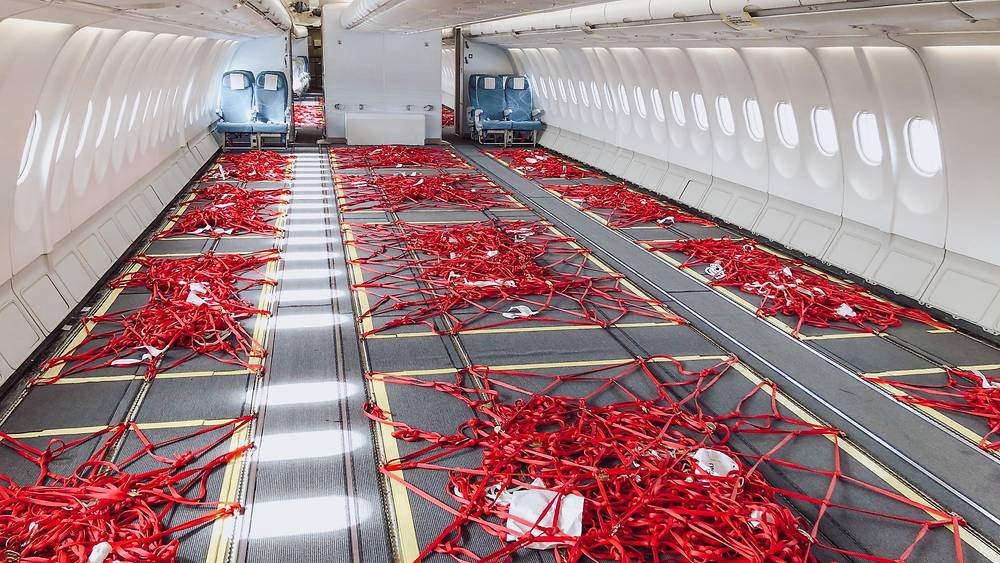
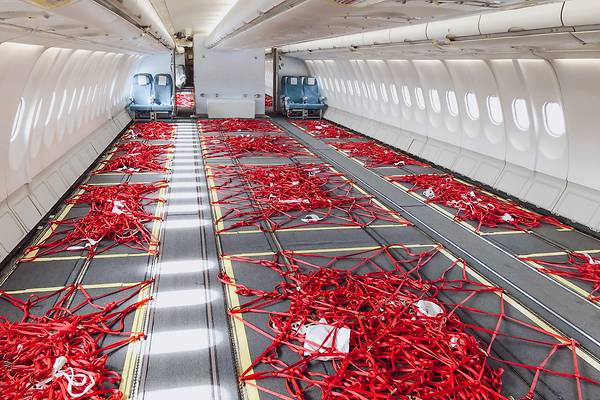
Protective equipment airlifted to Finland
At the height of the pandemic crisis, Finland was supplied with critically important protective equipment quickly and reliably via the combined efforts of Finnair and the National Emergency Supply Agency.
The National Emergency Supply Agency’s (NESA) Procurement Department Director Rain Mutka says that Finnair flew some cargo charter flights for HVK as early as the start of April, carrying much-needed face masks. The reason for using charter flights was the critical need for protective equipment: other forms of transport would have simply been too slow.
"Exceptional circumstances require exceptional methods"
- Fredrik Wildtgrube, Finnair
“As far back as April, Finnair coordinated deliveries and offered us their route expertise in the spirit of cooperation. At the start of May, we deepened our cooperation as due to the coronavirus situation Finnair was able to offer us the service of an expert familiar with airfreight operations,” Mutka says.
“He has been working for us on a purchased service contract since the start of May, coordinating not only air transports, but also land and sea transports and warehouse logistics. Such a direct link between us and Finnair has offered us a great opportunity for genuine win-win collaboration and provided us with expertise that we do not as extensively possess ourselves.”
The arrangement has made it possible to carry out transports very flexibly and efficiently.
“The possibility of using direct flights has ensured the safe supply of protective equipment. The number of flights has been high, with most of them flown by Finnair. Some of the aircraft were reserved exclusively for our use, while others transported jointly procured supplies for the NESA and hospital districts. On some occasions, we have also purchased only a portion of a plane’s total capacity.”
For the good of Finland
Mutka compares the airlifting of protective equipment in the spring to the ambulance flights flown from Thailand after the 2004 tsunami. Both endeavours serve as reminders of how important a national airline can be for a small country. The driving force behind the effort has been a desire to work together for the good of Finland.
“The possibility of using direct flights has ensured the safe supply of protective equipment.”
- Rain Mutka, National Emergency Supply Agency
“Finnair provided us with an employee in exchange for the assignment. He is familiar with the operations of both the NESA and Finnair – and airlines in general – and was able to coordinate them much more flexibly than two individuals each representing their respective organisation ever could have. In addition to coordination, we have been able to utilise his expertise in deciding which form of transport is the most suitable in each situation,” Mutka says.
“We have also been very meticulous in regard to addressing all the necessary conflicts of interest and other issues. We have made sure that our decision-making has always remained neutral, even when it comes to different form of transport.”
“The National Emergency Supply Agency’s approach of assembling experts from different organisations and quickly establishing effective procurement processes in a state of emergency is a great idea that is applicable to other types of emergencies as well.”
- Fredrik Wildtgrube, Finnair
At the NESA, knowledge of the special characteristics of airfreight is utilised throughout the procurement process. This is a novel approach, as according to Rain Mutka, procurement departments usually wait until the final stages of a procurement to decide on logistical processes because this kind of transparency simply doesn’t exist.
“At that point it’s a bit late. When it comes to successful procurement, it would be best to be aware of the logistics right from the start of the process. We are now transitioning to land and sea transports, but airfreight will remain an important tool in our arsenal. We will continue to utilise the logistical expertise gained from Finnair in the future as well.”
Finnair rose to the challenge
Finnair Cargo’s Head of Global Sales Fredrik Wildtgrube says that flight traffic is already gradually recovering and will continue to do so, barring any unexpected developments. In the spring, when the NESA proposed deepening their collaboration with Finnair, the situation was completely different. There was a global humanitarian crisis going on, and concern for the well-being of people in Finland was great.
“The situational picture was drafted over numerous discussions and very openly on both sides of the table, as we had a shared interest in addressing these issues in the best possible way. This thorough preparation allowed us to quickly find a successful and effective solution for supplying protective equipment.”
“One of the key strengths of our international virtual team was the ability to process information transparently and quickly and make decisions accordingly.”
- Mika Leppänen, Finnair
Finnair set out to look for an expert to send over to the NESA who could coordinate the flow of supplies and help communicate the NESA’s needs to airlines in a language that they would understand. The challenge was accepted by Head of Customer Experience Mika Leppänen.
“Within 48 hours of the first phone call, Mika was sitting at the NESA and thinking up solutions. Together we created a flexible operating model utilising Finnair’s direct connections to Asia, which made it possible to direct material flows to Finland reliably and at the right time,” Wildtgrube says.
“The National Emergency Supply Agency’s approach of assembling experts from different organisations and quickly establishing effective procurement processes in a state of emergency is a great idea that is without a doubt applicable to other types of emergencies as well. Our collaboration with the National Emergency Supply Agency has worked excellently.”
Transporting cargo with passenger aircraft
Under normal conditions, Finnair’s regular airline services carry both passengers and cargo. Since the company’s regular intercontinental airline service was suspended, the protective equipment transports were handled as pure cargo flights, the transport capacity of which was divided between customers based on demand. However, the flights still used existing flight numbers to the destinations in question and the flight and arrival schedules of the corresponding regular flights.
“The majority of the cargo has so far been transported using wide-body passenger aircraft, with the cabin empty. In some cases, it has also been possible to transport limited amounts of protective equipment in the cabin. Furthermore, two Airbus 330 aircraft were modified to serve as cargo planes with the removal of economy class seats. Passenger flights using wide-body aircraft are now slowly starting up again from July onwards, meaning that cargo traffic is being transformed back into regular scheduled service.”
The spring was exceptional in terms of the delivery profile as well.
“We do not normally fly aircraft chartered by a single customer, nor are the volumes of goods normally this high. Luckily we were commissioned to transport protective equipment to many other countries as well. We have been closely monitoring customers and demand, and consolidated our cooperation in carrying out of charter flights. When we identify an opportunity to fly with a customer, we go ahead and fly,” Wildtgrube summarises.
“We have been able to operate flexibly. Although requirements imposed by the authorities have been changing constantly, we have been able to adapt to the changes on as little as an hourly basis, when needed.”
“When it comes to precise logistics, all decision-makers must have constant access to equally up-to-date data.”
- Fredrik Wildgrube, Finnair
Logistics in a constantly changing environment
The pandemic has plunged the airline industry into the biggest crisis in the history of commercial aviation, which affects not only airlines themselves, but airports, ground service providers, agents and freight forwarders as well. On the other hand, these challenging conditions also offer opportunities for flexible operators, Wildtgrube points out.
“Exceptional circumstances require exceptional methods. Here at Finnair, we have been actively building new operating models utilising the geographical location of Finland in traffic between Europe and Asia. The key is to work together with both our own network partners and customers.”
The arrangement with the NESA provides an opportunity for precise and transparent dialogue, which is essential in the exceptionally rapidly changing logistical environment brought about by the pandemic.
“Supply and value chains are increasingly managed based on available data. However, at the height of the pandemic, that data and associated traffic volumes fluctuated rapidly, as a result of which issues such as points of congestion could form within mere minutes. And decisions had to be made accordingly. When it comes to precise logistics, all decision-makers must have constant access to equally up-to-date data. And that is what the liaison has played a vital role in ensuring.”
A tight-knit international team
Mika Leppänen from Finnair, who currently works for the National Emergency Supply Agency on a purchased service contract, says that the project faced a difficult start precisely because of the rapidly changing operating conditions. He points out that when an aircraft departs Finland, the presumption is that everything is already in order at the other end, in China.
“The cargo must be at the airport in Finnair Cargo’s facilities, declared and stacked on to pallets, ready to be loaded on to the aircraft. Before that, a local truck company has picked it up from the manufacturer’s factory or warehouse. Once the cargo is accepted at the forwarding company’s terminal for China’s customs declaration processes, the necessary documentation and a flight-specific loading plan are prepared, after which the cargo is finally transported to Finnair Cargo’s departure terminal,” Leppänen explains, describing the multi-faceted process.
“After the aircraft is loaded, the cargo is flown to Helsinki and unloaded into a Finnair Cargo COOL terminal, after which it is imported to Finland and the EU. The final step is to transport the cargo to the designated address.”
Leppänen praises the members of his virtual team, particularly Finnair Cargo’s personnel in China.
“They have worked around the clock when necessary to ensure seamless logistics. Our multinational and -lingual team also includes representatives of the forwarding company and transport companies, cooperation with whom has ensured that the goods have been successfully delivered to Finland on time.”
Up-to-date data is also required to optimise the capacity of each flight, for which end volumes and quantities must be known well enough in advance before transportation.
“If different operators do not operate based on the same situation picture, it is extremely difficult to succeed in all of this. In my opinion, one of the key strengths of our team was the ability to process information transparently and quickly and make decisions accordingly.”
Getting such a diverse group of people to work together seamlessly would not have been such an exceptional feat if everyone were part of the same organisation, Leppänen points out. Getting everyone to work together seamlessly required the virtual team to really go above and beyond, if only because of the various organisations each working in their own enterprise resource planning systems.
“In the end, we all had a shared interest and desire to resolve the practical challenges in the middle of the humanitarian crisis and provide protective equipment to the people of Finland.”
Images: Finnair and the National Emergency Supply Agency
Text: Jussi-Pekka Aukia