Cargo news
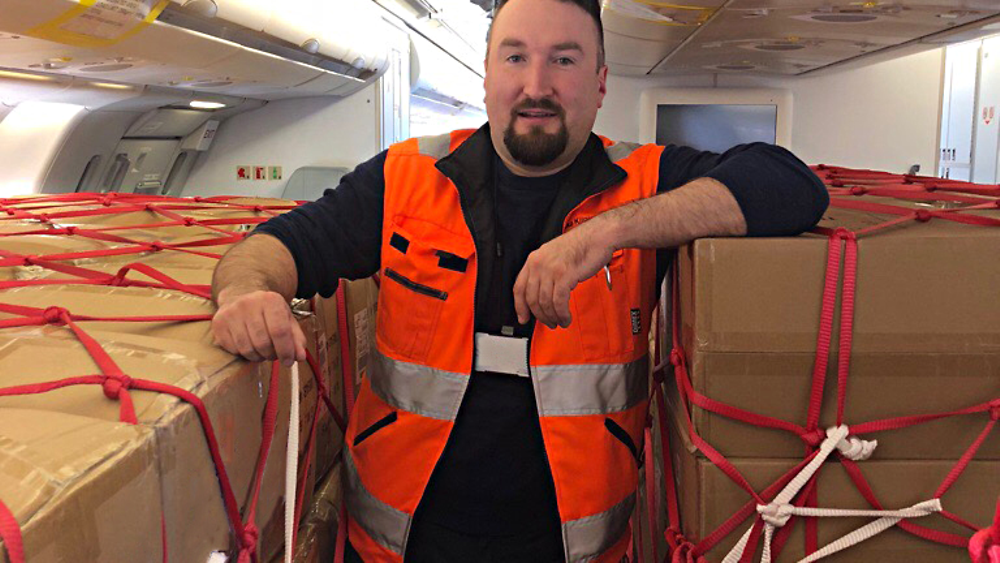
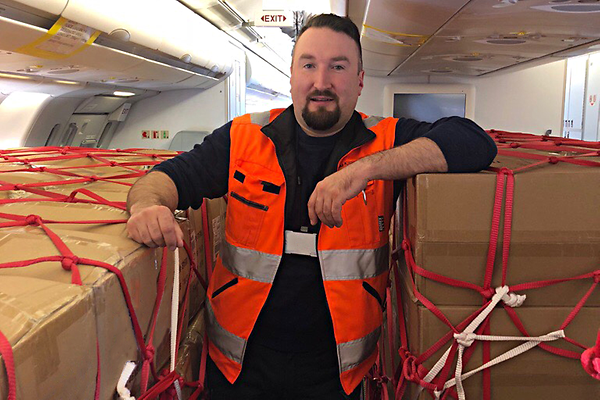
Behind the scenes: A330 modifications
This spring has been unusual for Finnair Cargo with Covid-19 impacting all sides of business. As the passenger traffic nearly stopped for a few months, it initiated a challenge for us at the cargo side: how can we keep our business going?
In early April, we started flying cargo-only flights with the A350 aircraft to several destinations in Asia, Europe and America, belly filled with cargo. From the first flight, we have increased dramatically to carry close to 60 long-haul cargo flights per week. While working with limited capacity in the cargo compartment, the passenger side of the plane was empty. Anyone with common sense would start to think if it was possible to also utilise the cabin space – normally reserved for passengers – for carrying cargo.
As aviation is filled with standards and regulations to ensure safety, we started to investigate different options of how to transform an Airbus A330 aircraft into a cargo freighter. After a few weeks of planning and removing the obstacles, Finnair was able to announce that two of its A330 aircraft were modified to transport double the amount of cargo on one flight.
What actually happened in the operations? Mika Kilpinen, Development lead for Operations, Quality and Compliance reveals what happened inside the aircraft during the transformation.
1. How long did it take to transform a passenger plane into a cargo freighter? How big was the transformation crew?
“It took about two weeks altogether, but the physical transformation took five working days from start to finish. We had an operation crew of about 10 team members working in 10-hour shifts during that week to make it happen from the operational side. Not to mention the countless hours of planning how to accomplish this!”
2. What were the technical changes you made?
“To use the cabin space for cargo, we removed Economy Class seats which took about two working days. During the transformation, we also removed other passenger-traffic-related equipment, such as the entertainment system, trollies and the crew resting module. We created 22 cargo areas that are secured by security nets. Each of those areas can carry 250 kg per square meter, between 600–1,400 kg and in volume 4–9 cubic meters. We utilised the same rail the passenger seats are fastened to secure the nets to hold the cargo load in place.”
3. What else did you need to consider from operational point of view?
“I guess the actual modification was relatively easy, once there was a plan on how to do it. When carrying cargo, the weight distributes differently compared to an aircraft with passengers: therefore, weight and balance calculations needed to be done and documented as well as testing and training. As this work is carried out in shifts, all manuals needed to be updated and all staff members trained to proceed with operations safely.
Airline operation is teamwork with many stakeholders in different sides of the organisation. This impacted changes for example in the load control processes, ground handling procedures and implementation, load master procedures and implementation, inflight supervision procedures and manuals and flight operation procedures and manuals. In this case, it was over 100 pages of manually written documentation and instructions!”
4. Where is cargo now being carried in the A330 aircraft?
"In addition to the normal belly cargo compartments, we can now carry cargo in the main deck in sections B and C, cabin storage compartments. The maximum load for these is 226 cubic meters, given the reality that cargo is always a particular shape. If cargo was, for example, water, the volume could be about 10% higher.”
5. What kind of cargo can be loaded onto the A330 freighter planes?
“We received permission from the authorities to use the passenger compartments to transport Covid-19-related supplies and cargo items that are vital for the functioning sensitive supply chains.”
6. How does it differ to fly cargo with a passenger plane vs. cargo freighter?
“On a real cargo freighter, the cabin structures, doors and loading systems are designed for loading and transporting cargo. On a passenger aircraft, we must use the passenger doors and the loading process is manual. More resources are needed for loading, and the size of the packages to be loaded is limited due to the manual process. We must be wary of the cabin upholstery and keep the plane tidy, as it will be converted back into a passenger aircraft later.
During the flight, there is always two cabin crew members and one load master to supervise the safety aspects during the flight. Depending on the route, flight times and schedules, there are up to six pilots on board to ensure safe flight operations. In case we depart immediately after loading in one of our long-haul destinations, we need three pilots to fly one way, so six in total.”
7. What was the most challenging about this project?
“Nothing like this has ever been done before at Finnair, so everything had to start from scratch. When aircraft changes like this are done for the first time, it has its own technical and operational challenges, and it is very time consuming. On the other hand, it was a challenge for us all which we took with passion and determination.”
8. What was best about this project?
“The project team was brilliant, committed and we could really sense that everyone was putting their 150% of effort into this. It was a real pleasure to work with so many Finnair colleagues in different departments and get to succeed together. We are very proud to see that everything is working perfectly, and we now have daily flights to Shanghai and Guangzhou with the new modified A330 aircraft.”