Cargo news
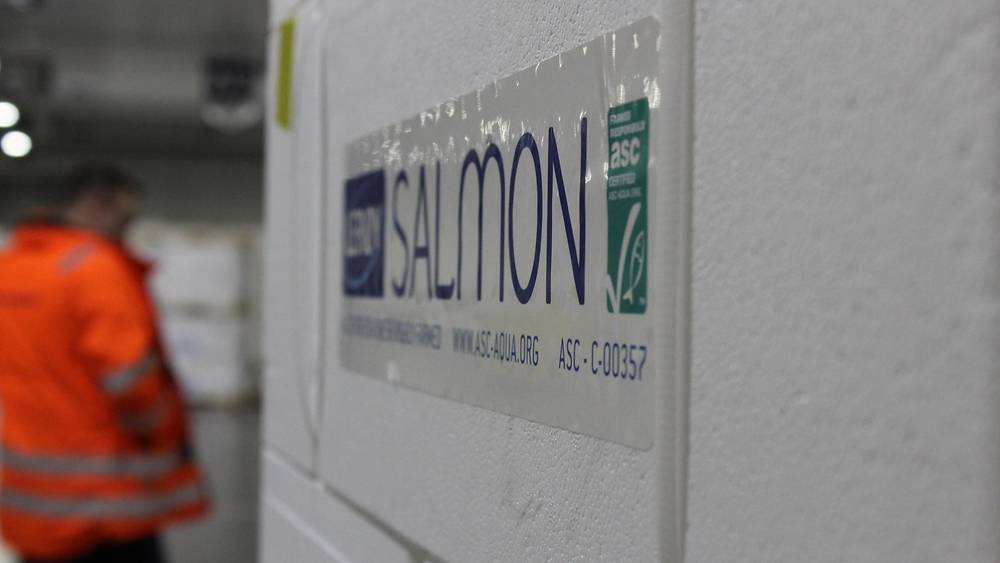
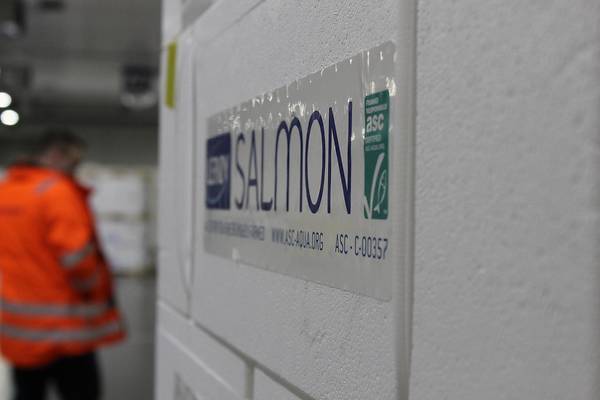
Finnair Cargo corrects Special Handling Code errors 50% faster in trial of new robotics technology
Reliable cargo deliveries depend on accurate documentation, and a critical part of that is the designation of the correct Special Handling Code (SPH) to a shipment. To prevent missteps during the entry process, Finnair Cargo has turned to robotic automation to lend a hand.
Today there are over 100 Special Handling Codes describing every type of cargo. SPH codes are typically entered manually in the air cargo industry – often by more than one person and via multiple electronic platforms – and that means the chance for an inaccurate code assignment is high, resulting in mismatched bookings and air waybills.
The administrative costs, delivery delays and lost cargo due to mis-assigned SPH codes is significant for the industry. Moreover, finding and correcting these errors is labour-intensive and time-consuming and air cargo carriers like Finnair Cargo shoulder the burden of these errors in the logistics chain.
Finnair has been addressing this issue using a new approach, called Robotic Process Automation (RPA), and results from a recently concluded proof-of-concept pilot are encouraging.
Getting the data right
“The assignment of correct SPHs is essential for two reasons,” explains Petteri Hellén, Development Lead for Finnair Cargo’s Operations Systems. “We naturally want to ensure that cargo is handled correctly at each point along the delivery chain.”
For example, refrigerated cargo heading to the COOL Nordic Cargo Hub at Helsinki Airport could have been assigned any one of four SPH codes – CRT, ERT, COL and FRO – each with a different temperature specification. Getting the code correct in the documentation is crucial to ensure that the refrigerated cargo, be it pharmaceuticals, fish or agricultural products, is delivered to the right location to prevent spoilage.”
“Secondly, our SkyChain ERP (Enterprise Resource Planning) system recognises discrepancies between a cargo booking and its corresponding air waybill and will not process a shipment until this is resolved,” Hellén points out. “The problem is typically due to missing or mis-assigned SPH codes. This delay in processing the cargo shipment can be costly.”
The frequency of mis-assigned SPH codes, along with other deviations in air waybill data is significant, affecting as much as a third of all cargo shipments. Given the extent of the problem, a new approach was needed.
Pilot validates use of robotics
In November of 2017, Finnair Cargo investigated the applicability of robotics to assist in identifying and resolving SPH code errors in shipping documents as well as other process-intensive functions that currently use human labour.
“Our search brought us to Finland-based Digital Workforce,” says Kari Saarikoski, who leads digital transformation at Finnair Cargo. “Their expertise in RPA and track record in software robotics was a good fit for our needs.”
Digital Workforce describes themselves as “the only Nordic company specialising in Intelligent process automation services on an industrial scale”.
According to Saarikoski, collaboration with Digital Workforce commenced in March of this year, resulting in the launch of a proof-of-concept pilot for Finnair Cargo.
“The idea of the pilot was to implement a robotic automation platform capable of identifying and resolving SPH code issues faster and more accurately than can be done by humans,” says Ashish Desai, IT Development Manager for Cargo Applications.
“The software robot can run virtually 24 hours a day, doing tasks that are considered tedious for humans but optimal for machines. This allows us to free-up personnel to focus on other tasks where human skills are better suited.”
Desai reports that late-stage results from the pilot yielded solid results.
“There are many data elements associated with a cargo shipment, but for those discrepancies in documentation that are purely SPH code-related, we are achieving a clearly better success rate,” notes Desai. “We also learned that the robot can resolve other non-SPH code discrepancies, such as conflicts in business rules.”
On average, Finnair Cargo estimates that the robot needs only 50% of the time it takes a human to do the same processing.
Wider rollout foreseen
In late September 2018, the cargo pilot was concluded, and full RPA implementation is currently underway.
“We have now proven this works,” points out Saarikoski, “and we have moved into full production. Indeed, we have also applied the same RPA platform in two similar pilots in Finnair – one in finance and the other Tech OPS, and are expecting positive results there, too.”
In a Nutshell
- The accurate entry of Special Handling codes (SPH) in cargo shipping documentation is essential to timely and successful transport.
- As many as one-third of all air waybills require additional action or correction due to missing or mis-assigned SPH codes and other air waybill data.
- The process of correcting SPH code errors in cargo shipping documentation is labour-intensive, mundane, time-consuming and expensive.
- Finnair Cargo has turned to Robotic Process Automation (RPA) to solve this challenge.
- Collaborating with Finland-based Digital Workforce, a proof-of-concept pilot was held this year. Results of the pilot were successful, and full implementation of the RPA robot is now underway.
- Finnair views RPA as a viable solution in other areas of operations.